The Definitive Guide to Alcast Company
The Definitive Guide to Alcast Company
Blog Article
10 Simple Techniques For Alcast Company
Table of ContentsThe Greatest Guide To Alcast CompanySome Known Factual Statements About Alcast Company Some Known Incorrect Statements About Alcast Company Alcast Company Fundamentals ExplainedThe 6-Second Trick For Alcast CompanyEverything about Alcast Company
Chemical Comparison of Cast Aluminum Alloys Silicon promotes castability by decreasing the alloy's melting temperature and enhancing fluidity during casting. Furthermore, silicon contributes to the alloy's stamina and use resistance, making it important in applications where toughness is crucial, such as automotive components and engine elements.It also enhances the machinability of the alloy, making it easier to refine into ended up products. In this means, iron adds to the total workability of aluminum alloys. Copper raises electrical conductivity, making it useful in electric applications. It also enhances corrosion resistance and contributes to the alloy's total toughness.
Manganese adds to the stamina of light weight aluminum alloys and enhances workability (aluminum foundry). It is frequently used in wrought aluminum items like sheets, extrusions, and profiles. The visibility of manganese help in the alloy's formability and resistance to breaking throughout fabrication processes. Magnesium is a light-weight element that gives toughness and effect resistance to light weight aluminum alloys.
The Only Guide for Alcast Company
Zinc enhances the castability of aluminum alloys and helps manage the solidification procedure during casting. It enhances the alloy's stamina and firmness.
The primary thermal conductivity, tensile strength, return strength, and elongation vary. Among the above alloys, A356 has the highest thermal conductivity, and A380 and ADC12 have the least expensive.
The Only Guide to Alcast Company
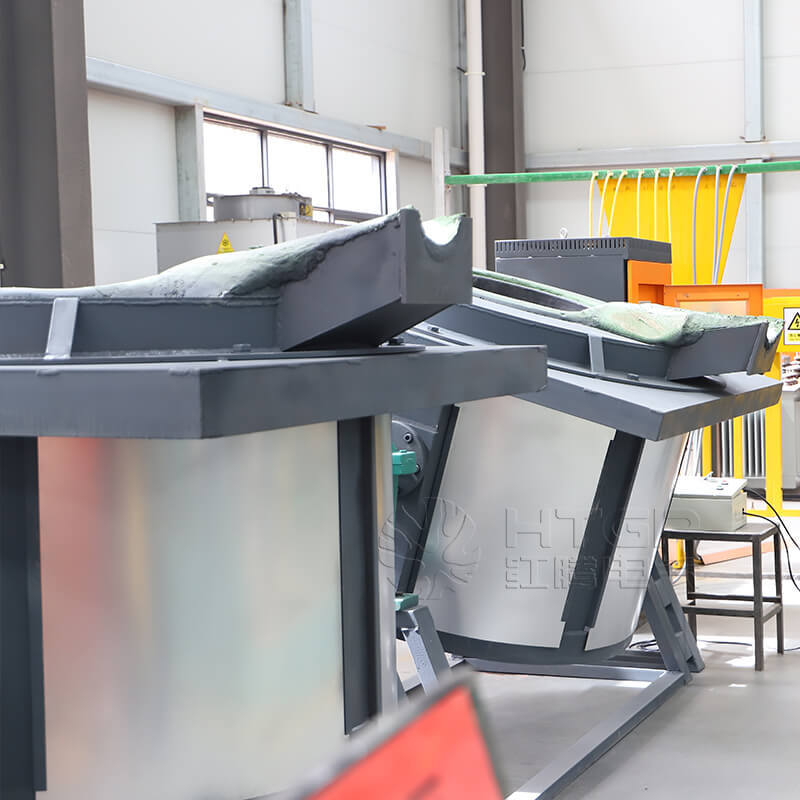
In precision spreading, 6063 is fit for applications where complex geometries and premium surface area finishes are critical. Examples consist of telecommunication website link enclosures, where the alloy's remarkable formability permits smooth and aesthetically pleasing designs while preserving structural stability. In the Illumination Solutions market, precision-cast 6063 parts produce sophisticated and reliable illumination fixtures that call for complex forms and excellent thermal efficiency.
The A360 exhibits superior prolongation, making it excellent for complicated and thin-walled elements. In precision casting applications, A360 is appropriate for sectors such as Customer Electronics, Telecommunication, and Power Tools.
Our Alcast Company Diaries
Its special residential or commercial properties make A360 a useful choice for precision spreading in these markets, enhancing item resilience and quality. aluminum foundry. Light weight aluminum alloy 380, or A380, is an extensively made use of spreading alloy with several distinctive qualities.
In precision spreading, aluminum 413 beams in the Customer Electronic Devices and Power Tools industries. It's commonly used to craft intricate parts like smart device real estates, cam bodies, and power device coverings. Its accuracy is impressive, with tight resistances as much as 0.01 mm, making sure perfect item assembly. This alloy's exceptional corrosion resistance makes it an outstanding choice for outdoor applications, making certain durable, resilient products in the stated markets.
Alcast Company - Truths
As soon as you have determined that the light weight aluminum die casting procedure is suitable for your job, an essential next action is choosing one of the most appropriate alloy. The aluminum alloy you choose will substantially impact both the spreading procedure and the properties of the last product. Due to this, you must make your decision very carefully and take an informed technique.
Figuring out the most appropriate aluminum alloy for your application will indicate considering a large variety of qualities. The very first category addresses alloy features that influence the manufacturing procedure.
Alcast Company Fundamentals Explained
The alloy you choose for die spreading directly affects numerous aspects of the spreading process, like exactly how simple the alloy is to work with and if it is susceptible to casting defects. Warm breaking, additionally called solidification splitting, is a typical die spreading problem for aluminum alloys that can cause internal or surface-level splits or cracks.
Particular aluminum alloys are a lot more susceptible to hot cracking than others, and your choice must consider this. Another common defect discovered in the die spreading of light weight aluminum is pass away soldering, which is when the actors sticks to the die walls and makes ejection hard. It can harm both the actors and the die, so you must try to find alloys with high anti-soldering properties.
Deterioration resistance, which is currently a significant characteristic of light weight aluminum, can differ substantially from alloy to alloy and is a vital characteristic to think about relying on the ecological problems your product will be exposed to (aluminum casting manufacturer). Use resistance is an additional residential or commercial property frequently sought in light weight aluminum products and can set apart some alloys
Report this page